Apparel Industry Braces Itself for a Hike in Quality Issues Due to Coronavirus Backlog
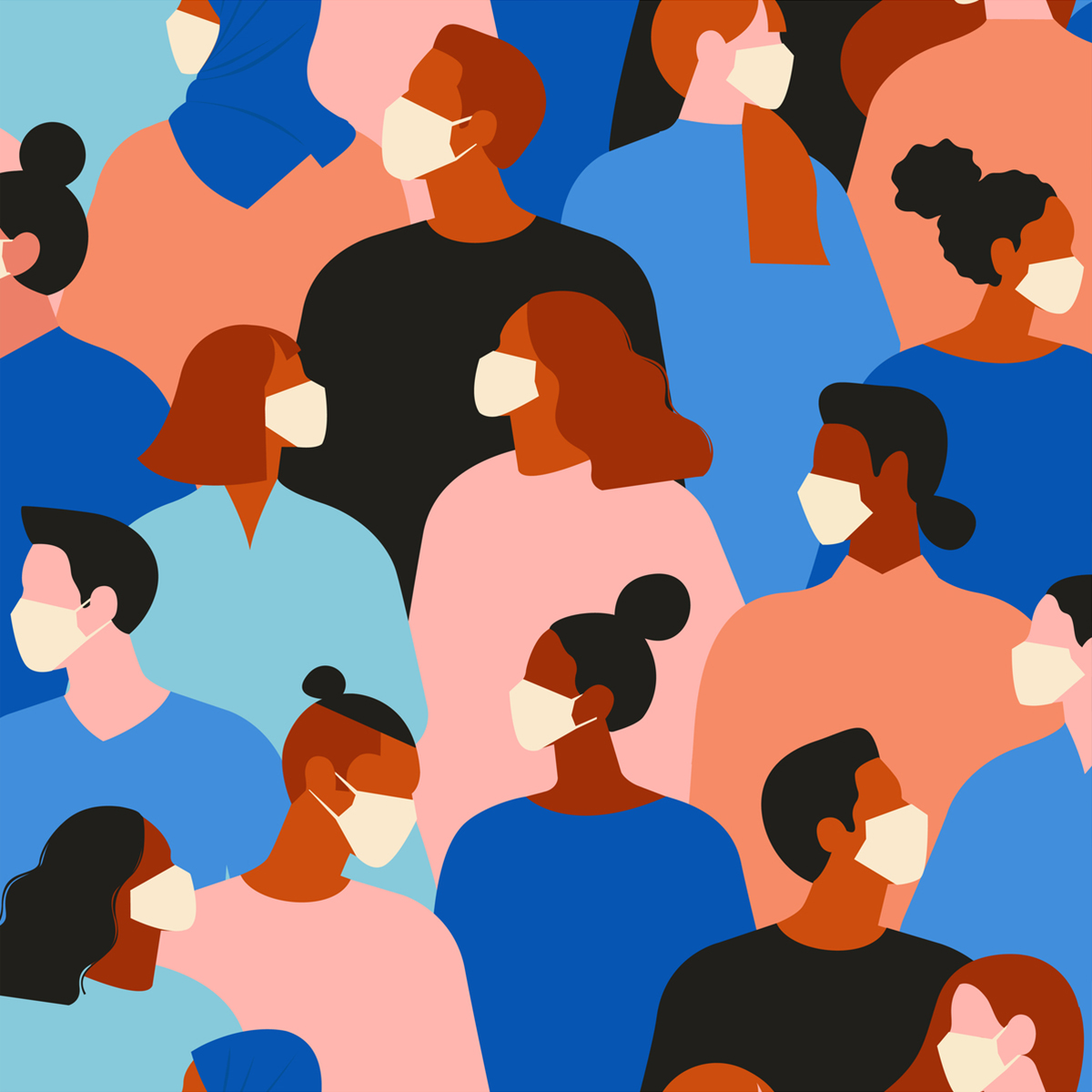
Every year after the Chinese New Year holiday, the garment industry experiences a marked drop in quality levels and conformity to order specifications, recorded at pre-shipment inspection.
A high post-CNY worker turnover rate as well as workers’ delayed return to the factories mean that manufacturers are not able to operate at full capacity upon reopening. Inexperienced workers require training which contributes further to the backlog as well as increasing the instances of quality issues in both raw materials and garment production.
Factories are under increased pressure to fulfill orders which can lead to rushed and/or substituted raw materials production (especially a problem for complex product), a lack of time to conduct proper internal QC processes and an increase in unapproved subcontracting. Late or misleading information from factories regarding quality or production scheduling issues can leave little or no opportunity to find solutions or fix defects.
All of this not only affects quality, but also the brand/retailer’s ability to deliver on its sales and CSR commitments.
This year, the extension of the CNY closures as well as the uncertainty associated with the coronavirus will put additional pressure and increased risk on the entire supply chain, not only in China but also across the region as a whole.
Restrictions are now being removed and many factories have already reopened. There is however a lot of uncertainty regarding when factories will be operating at full capacity and when orders can be fulfilled and shipped. Brands and retailers are all pushing to get their orders prioritized but information is changing every day and getting visibility on production and shipment dates is a huge challenge.
What can brands/retailers do to reduce their risk?
- Ensure they have a presence in the factories
- Increase quality inspections – both fabric and garments
- Conduct inspections and quality control measures earlier in the process (eg pre-production meeting, inline inspection)
- Closely monitor production scheduling updates with the factory
How can Happy Rabbit help?
We support brands and factory staff to make decisions that are in the interest of both brand protection and the long-term relationship between supplier and factory.
Through boots on the ground combined with a user-friendly tech platform we offer our customers a high level of real-time visibility as well as the possibility of data-driven insights and performance analytics over time. The onboarding process is simple and fast and reporting is carried out efficiently through the customers’ personalized portal.
Many of our customers are currently ramping up their presence in the factories in order to manage this period and are focusing on the following two main areas:
1. WIP follow up
Through Work-in-Progress (WIP) tracking, we monitor the schedule to ensure that raw material deliveries are on track, styles are prioritized and delays are anticipated in good time. We work to ensure that confirmed ex-factory dates are maintained.
2. Quality control processes
We conduct pre-production meetings and raw materials inspections as well as inline and end line inspections. We check that orders are executed at the approved facility and offer guidance with solutions to quality issues highlighted.
Happy Rabbit will continue to monitor the coronavirus situation and will be posting updates. In the meantime, we welcome brands/retailers to reach out to us if they have any questions or concerns.
For more information about how we can help, please contact us.